Leading Liquid Packaging Machine Supplier for Industry-Specific Solutions
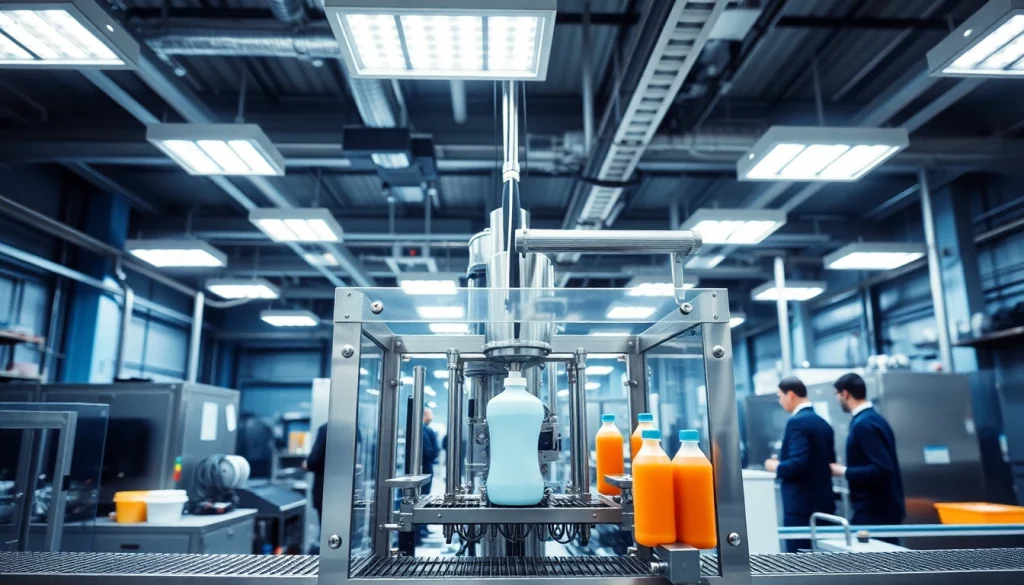
Understanding Liquid Packaging Machines
What is a Liquid Packaging Machine?
A liquid packaging machine is a specialized apparatus designed for the efficient and accurate packaging of liquid products. These machines can handle a variety of liquids, from water and juices to oils and chemicals, adjusting to specific viscosity requirements and packaging types. Typically, a liquid packaging machine automates the process of filling, capping, and labeling containers, significantly streamlining production lines.
The technology behind these machines varies, but they generally operate through filling mechanisms such as gravimetric, volumetric, or piston filling systems, depending on the product’s characteristics and the required accuracy. Companies in industries ranging from food and beverages to pharmaceuticals invest in these machines to enhance productivity, reduce labor costs, and maintain high standards of hygiene and safety. For businesses seeking to enhance their operations, sourcing from a reliable Liquid Packaging Machine Supplier is crucial.
Types of Liquid Packaging Machines
Liquid packaging machines come in various types, tailored to meet the specific requirements of different industries. Below are some of the most common types:
- Gravity Filling Machines: Ideal for low-viscosity products, gravity filling machines use gravity to flow liquids from a tank into the container. These are cost-effective and easy to operate.
- Piston Filling Machines: These machines use a piston mechanism to accurately fill containers. They are suitable for thick liquids and pastes such as creams and sauces.
- Vacuum Filling Machines: Vacuum technology is used to fill containers while minimizing air exposure, which is particularly beneficial for sensitive products like oils and juices.
- Rotary Filling Machines: Rotary machines are highly efficient and suitable for high-volume production. They can handle various bottle shapes and sizes and are commonly used in the beverage industry.
- Inline Filling Machines: These machines offer flexibility in production and are capable of filling a range of containers by adjusting guides and settings.
Common Applications and Industries
Liquid packaging machines are used across a multitude of industries, each with distinct requirements:
- Food and Beverage: From filling juice bottles to packaging sauces, the food and beverage industry is one of the largest users of liquid packaging machines. Hygiene and speed are critical in this sector.
- Pharmaceutical: Accuracy and sterility are paramount in pharmaceutical applications. Machines must adhere to strict regulations and ensure proper dosing for liquid medications.
- Chemical: The chemical industry requires machines that can handle harsh substances safely, accommodating special machinery materials resistant to corrosion.
- Cosmetics: Liquid packaging in the cosmetics industry often involves a variety of container shapes and sizes, necessitating adaptable machines that can handle different viscosities.
Choosing the Right Supplier
Factors to Consider When Selecting a Supplier
When choosing a liquid packaging machine supplier, various factors come into play that can impact your overall production efficiency:
- Product Range: A supplier should offer a diverse range of machines that can accommodate different liquid types and packaging formats.
- Customization Options: The ability to customize machines to meet your production requirements is crucial for achieving optimal efficiency.
- Technical Support: Reliable post-sale support, including installation, training, and maintenance services, should be part of the package.
- Lead Times: Quick turnaround times for machine delivery and installation can help minimize downtime and get production up and running faster.
- Cost of Ownership: Consider not just the initial purchasing cost but also maintenance, running costs, and expected lifespan of the equipment.
Evaluating Supplier Reputation and Experience
Assessing the reputation of potential suppliers is essential in ensuring a smooth purchasing process:
- Industry Experience: Suppliers with years of experience may have encountered and solved challenges that newer companies might still struggle with.
- Customer Feedback: Research reviews, case studies, and testimonials from previous clients to gauge satisfaction.
- Certifications: Certifications from relevant industry bodies can confirm a supplier’s commitment to quality and compliance with industry standards.
- Partnerships: Existing relationships with other reputable companies can indicate trustworthiness and reliability.
Cost vs. Quality: Finding the Right Balance
In any manufacturing investment, striking a balance between cost and quality is key. Here’s what to consider:
- Initial Investment: Lower-cost machines may save money upfront but may require more maintenance or have shorter lifespans.
- Quality of Materials: The durability and reliability of machine components will usually correlate with the cost.
- Efficiency vs. Price: High-efficiency machines may have a higher price point but can result in lower operational costs in the long run due to reduced waste and faster production speeds.
Latest Innovations in Liquid Packaging Technology
Trends Shaping the Future of Packaging
The liquid packaging industry continues to evolve with the advent of new technologies and changing consumer preferences:
- Smart Packaging: Technologies such as IoT-enabled machines allow for real-time monitoring and data analysis to optimize production lines.
- Flexible and Eco-Friendly Materials: The push for sustainability has intensified, leading to innovations in biodegradable and recyclable materials.
- Customization and Personalization: Brands are increasingly looking to provide personalized packaging solutions that better resonate with individual customers.
Benefits of Automated Systems
Automation plays a pivotal role in today’s liquid packaging solutions. Here are some critical advantages:
- Increased Efficiency: Automated systems can operate continuously without breaks, significantly boosting output rates.
- Consistency: Automation ensures that each fill is consistent in terms of volume, reducing variances that can occur during manual filling.
- Reduced Labor Costs: Fewer staff are needed to operate machines, allowing for reallocating resources to other areas of the production process.
Integrating Sustainability into Packaging Solutions
As companies become more environmentally conscious, integrating sustainable practices into packaging becomes imperative:
- Use of Recyclable Materials: Many manufacturers are shifting towards using recyclable materials for their packaging to attract eco-conscious consumers.
- Energy Efficiency: Investing in energy-efficient machines can reduce overall power consumption in production processes.
- Waste Minimization: Deploying machines that minimize product waste during the filling process helps reduce the ecological footprint of manufacturing.
Best Practices for Machine Operation
Maintenance Tips for Longevity
Proper maintenance of liquid packaging machines is critical for ensuring longevity and peak performance:
- Regular Inspections: Scheduled inspections can identify wear and tear before it leads to significant breakdowns.
- Proper Cleaning: Maintaining hygiene is crucial, especially in food and pharmaceutical industries. Implement cleaning schedules for parts in contact with products.
- Replace Worn Parts Promptly: Attending to worn or damaged components can prevent operational downtime and preserve efficiency.
Training Staff for Optimal Performance
Even the most advanced machines require skilled personnel to operate effectively:
- Comprehensive Training Programs: Provide detailed training for all staff on proper machine operation and troubleshooting protocols.
- Cross-Training: Ensure multiple team members are trained in machine operation to maintain flexibility in staffing.
- Update Training Regularly: As machines evolve, ensure training programs are updated to reflect new technologies and processes.
Safety Protocols for Operation
Safety should always be a top priority in any manufacturing setting, including liquid packaging:
- Conduct Regular Safety Audits: Schedule audits to ensure compliance with safety regulations and to identify potential hazards.
- Provide Personal Protective Equipment: Ensure that all operators have access to appropriate safety gear, such as gloves and eyewear.
- Emergency Procedures: Establish clear emergency procedures and regularly train staff on how to respond in case of accidents.
Case Studies of Successful Implementations
Industry-Specific Success Stories
Examining case studies from various industries can yield useful insights on successful liquid packaging implementations:
- A Beverage Manufacturer: A leading beverage company increased its output by 30% after integrating an automated filling system, enabling them to meet growing demand without compromising quality.
- A Pharmaceutical Company: An organization adopted a high-precision piston filling machine, eliminating discrepancies in dosage and significantly enhancing compliance with pharmaceutical standards.
- A Cosmetic Brand: By switching to a flexible liquid packaging machine, a beauty products brand managed to introduce personalized packaging, resulting in a 15% increase in sales.
Lessons Learned from Leading Companies
Several key lessons come from successful companies in the liquid packaging field:
- Adaptation to Market Changes: Companies that remain adaptable and proactive can leverage new technologies to gain a competitive edge.
- Investing in Quality Equipment: High-quality machinery correlates directly with reduced downtime and maintenance costs.
- Continuous Improvement: Emphasis on innovation and improvement enabled leading firms to stay at the forefront of packaging technology.
Impact on Efficiency and Cost-Effectiveness
Investing in the right liquid packaging solutions has a pronounced effect on operational efficiency:
- Increased Throughput: Companies report that upgrading to automated packaging solutions has led to substantial increases in throughput.
- Reduced Labor Costs: Automation allows fewer labor resources to achieve production goals, effectively lowering operating costs.
- Minimized Waste: Modern machines’ efficiencies help to minimize waste and product loss, thus increasing profitability.