Understanding Thermal Management Materials: Functions, Types, and Applications
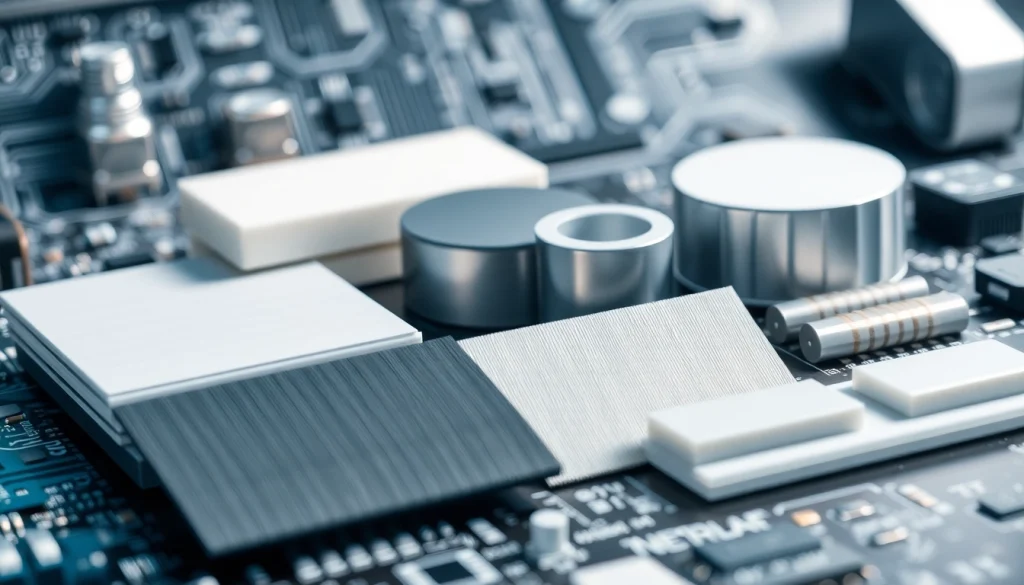
Overview of Thermal Management Materials
In modern electronics, managing heat efficiently is essential to ensure optimal performance, longevity, and safety. This is where thermal management materials come into play. These materials are specifically designed to dissipate heat generated by electronic components, enabling effective thermal management across various applications, from consumer electronics to industrial devices.
What are Thermal Management Materials?
Thermal management materials (TMMs) refer to a wide array of specialized materials employed to facilitate effective heat dissipation within electronic systems. They include thermal interface materials (TIMs), gap fillers, thermal adhesives, and gels, among others. The primary function of these materials is to enhance heat transfer from the heat-generating components to other areas that can disperse heat more effectively, thus preventing thermal buildup which can lead to reduced performance or failure of the electronic devices.
Importance in Electronics
As electronic devices become more compact and high-powered, the heat generated during their operation has increased significantly. Effective thermal management is crucial not only for maintaining performance but also for ensuring the safety and reliability of devices. Overheating can lead to failures, reduced lifespan, and potential hazards like fires. Consequently, the integration of TMMs is vital in sectors such as automotive, aerospace, consumer electronics, and telecommunications, making them indispensable in electronics design and manufacturing.
Range of Applications
Thermal management materials are utilized across a variety of fields, including:
- Consumer Electronics: Smartphones, laptops, and gaming consoles rely on TMMs to maintain performance and comfort.
- Automotive: Electric vehicles (EVs) utilize these materials for battery management and other heat-sensitive components.
- Aerospace: Components in aircraft demand high-performance thermal management due to extreme environmental conditions.
- Telecommunications: TMMs are crucial for managing heat in data centers and network equipment.
Types of Thermal Management Materials
Understanding the different types of thermal management materials is key to selecting the appropriate option for specific applications. Here, we delve into several common types of TMMs:
Thermal Interface Materials (TIM)
TIMs serve as conduits for heat transfer between surfaces, significantly reducing thermal resistance. They are used where two solid components are in contact and require enhanced thermal conductivity. Key varieties include:
- Thermal Greases: These are liquids containing thermally conductive fillers, used to fill microscopic gaps between surfaces.
- Phase Change Materials (PCMs): These materials absorb heat without a significant increase in temperature until they transition from solid to liquid, effectively managing heat spikes.
Gap Fillers and Pads
Gap fillers and pads are designed to fill spaces between heat-generating components and heat sinks, enhancing heat dissipation. These materials compress under pressure, forming a solid connection that promotes heat transfer. Gap fillers can be classified as:
- Soft Gap Pads: These materials provide excellent thermal conductivity while also accommodating movements between components.
- Rigid Gap Fillers: These are typically used in applications requiring a strong bond and structural support.
Thermal Adhesives and Gels
Thermal adhesives combine bonding and thermal management capabilities, making them ideal for securing components while facilitating heat transfer. Thermal gels also fall into this category, offering superior heat conduction with flexible application options. They are particularly useful in irregularly shaped or high-precision applications.
Selection Criteria for Thermal Management Materials
Selecting the right thermal management material is essential for achieving optimal thermal performance. Here are some important criteria to consider:
Key Performance Metrics
When choosing TMMs, several performance metrics must be evaluated, including:
- Thermal Conductivity: This measures the material’s ability to conduct heat, often expressed in watts per meter-kelvin (W/mK). Higher values indicate better performance.
- Thermal Resistance: Represented as °C/W, lower thermal resistance values suggest more efficient heat transfer.
- Mechanical Properties: Flexibility, compressibility, and adhesion strength are crucial to ensure that the materials remain effective during thermal expansion or contraction.
Material Compatibility
Compatibility with the components involved is critical in selecting thermal management materials. The chosen materials should adhere well to surfaces and be chemically stable, especially in environments where reactive substances may be present. It’s vital to conduct compatibility tests, ensuring that the TMMs do not degrade or react adversely when in contact with various substrates.
Environmental Considerations
Many applications necessitate thermal management materials that can withstand harsh environmental conditions such as extreme temperatures, humidity, and exposure to chemicals. The long-term stability and performance of TMMs should be assessed in relation to their operating environment. Additionally, considerations around sustainability and environmental impact, such as the recyclability or biodegradability of materials, have become increasingly important.
Best Practices for Implementing Thermal Management Solutions
To ensure effective thermal management, following best practices during application and implementation is essential. Here are some key considerations:
Application Techniques
Proper application of thermal management materials is crucial. Techniques may vary depending on the type of material used:
- Spread Techniques: For thermal adhesives and greases, uniform application across the surface area is necessary to eliminate air pockets that hinder thermal conduction.
- Pressure Application: For gap fillers and pads, ensuring appropriate pressure during assembly maximizes contact and promotes efficient heat transfer.
Testing and Validation Methods
Once thermal management materials are applied, rigorous testing must be conducted to validate their effectiveness. Common testing methods include:
- Thermal Imaging: Using thermal cameras to visualize heat flow and identify hotspots during operation.
- Thermal Cycle Testing: Subjecting materials to extreme temperature changes to evaluate their stability and performance under operational conditions.
Case Studies and Success Stories
Real-world applications can provide insight into the successful implementation of thermal management solutions. One notable example includes the use of thermal gap fillers in electric vehicle batteries, where efficient heat dissipation is critical for performance and safety. By implementing advanced gap filler materials, manufacturers have been able to enhance battery life and energy efficiency, demonstrating the transformative impact of effective thermal management.
Future Trends in Thermal Management Technologies
The field of thermal management is rapidly evolving, driven by the increasing demand for more efficient electronic systems. Here are some anticipated trends:
Innovation in Material Development
Continued advancements in material science will likely lead to the development of more effective thermal management materials. Innovations such as nanomaterials and advanced composites are on the horizon, offering enhanced thermal conductive properties along with lightweight characteristics, which is particularly appealing in sectors like automotive and aerospace.
Impact of Electric Vehicles
The rise of electric vehicles presents unique thermal management challenges and opportunities. The high-performance requirements for EV battery systems necessitate innovative TMMs that can operate efficiently in compact spaces while managing heat effectively. As the EV market continues to grow, so will the emphasis on developing specialized thermal materials that cater to these requirements.
Market Predictions and Growth Opportunities
The global demand for thermal management materials is expected to rise as more industries recognize the importance of effective heat management. Analysts predict substantial growth in the market, driven by ongoing technological advancements, particularly in consumer electronics, automotive, and industrial applications. Companies that prioritize R&D in thermal materials will likely position themselves favorably in this expanding market.